Keynote Speakers
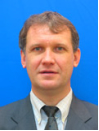
Radio Frequency IDentification in Supply Chain: Technology, Applications and Trends
Professor Alexandre Dolgui is Full Professor of Exceptional Class la Ecole des Mines de Saint-Etienne, Deputy Director for Research of Institute Henri
Fayol / Director of Laboratory for Information Science and Technology. His areas of scientific interests are: Optimal Design of Production and Assembly Lines,
Inventory Control and Supply Chain Optimization,
Planning and Scheduling,
Computer-Aided Process Planning Solutions,
Discrete Optimization Methods,
Discrete-Event Simulation.
He is chair of IFAC Technical Committee "Manufacturing Modelling for Management and
Control"; Member of IFAC Technical Committee "Manufacturing Plant Control", chair of
working group "Design and control of reconfigurable manufacturing systems".
Professor Dolgui has published more than 400 refereed journal and conference papers, book chapters and research reports.
Abstract: In this presentation, first the main characteristics of RFID technology are provided. It is showed that RFID is a big step forward when compared to bar codes. Since this is an emerging technology, a succinct guideline for its deployment is proposed. Existing and conceivable applications, as well as industrial sectors that already use the technology are presented. A particular attention is paid to use of RFID to improve the efficiency of supply chains. Two unavoidable subjects are discussed: privacy concerns and the corresponding protection strategies, as well as authentication that, in particular, include the problem of misbehaving tags.
Professor Marco Ceccarelli, University of Cassino, Italy
Trends and Challenges in Research for Service Robots
Marco Ceccarelli is Professor of Mechanics of Machinery and Director of LARM, the Laboratory of Robotics and Mechatronics at the University of Cassino. He is member of Commission for Robotics of IFToMM, the International Federation for the Promotion of Machine and Mechanism Science. He has written the books “Fundamentals of Mechanics of Robotic Manipulation” published by Kluwer in 2004 and “Mecanismos” published by Trillas in Mexico in 2008. He has been President of IFToMM for term 2008-2011. His research interests cover aspects of Mechanics of Mechanisms and Robots, History of TMM, and Mechanism Design. He is author or co-author of more than five hundred papers, which have been presented at Conferences or published in national and international journals, and he has edited 16 books as for conference proceedings and specific topic issues.
Abstract: Service robots give the possibility of new fields of applications for Robotics by wide spreading robots also into non technical areas. But new requirements and goals need to be carefully considered both in designing and operating specific solutions. In this lecture, main aspects and challenges are discussed both as problems and advantages in developing and using robots in service operations for new areas of applications, by taking particular attention to non engineering aspects that are deduced from new service areas. Key problems for developing service robots for a successful acceptance and use by even non technical users can be considered in terms of specific technical problems for low-cost user-oriented operation systems, but mainly in terms of implications for human-machine interactions.
Professor Hector Puyosa, SABIC, Cartagena, Spain
Service innovation to drive chemical operation efficiency
Hector Puyosa has more than 25 years of experience on service, oil & gas and plastic industries. He started his career in 1984 as maintenance electronic and automation engineer providing services for companies on food, beverage, paper and metal transformation sectors. He moved to the oil and gas industry in 1991, working for the Venezuela's national oil company, PDVSA, as process automation engineer. He entered in the plastic business in 1996 as senior process engineer for the design and implementation of the control system for the largest polycarbonate plant built in Spain. He currently works as chemical operation plant manager at SABIC Cartagena. Hector led a GE Plastics global initiative on advanced manufacturing system as technical leader setting priorities and direction around MES and control system, identifying focus group activities and developing metrics of success, defining global standards and process/procedure to retain business knowledge. Hector has a Ph.D. degree on Industrial Engineering from the University of Murcia and is partial-time professors at Polytechnic University of Cartagena.
Abstract: Chemical companies are facing tough challenges to compete in a global economic world with overcapacity, high raw material prices and increased product commoditization. Maintain competitive advantages requires to have in place a continuous improvement process to monitoring key business performance indicators, identify business strengths and weakness and timely take actions to maximize profit by efficient production and distribution of goods
Purpose of this talk is to present an industrial example on how service science could be applied to sustain chemical operation efficiency by integrating knowledge and systems. Knowledge from operation, engineering, maintenance and process control domains is combined with a so called Advanced Manufacturing System toolkit to improve asset efficiency, optimize plant operation and retain people knowledge. Description of what type of plant data and systems are needed to capture, storage and exchange relevant information to understand process variance, plant uptime and asset availability will be discussed. Lesson learned during execution of this program and identified gap and potential opportunities to create service innovation for chemical operation efficiency is also shared.
Christoph Legat, Siemens AG, Munich, Germany
Knowledge-based Technologies for Future Factory Engineering and Control
Christoph Legat studied computer science and business administration at the University of Munich, Germany. For more than four years, he is working for the Siemens AG and is currently with the research group for reasoning and distributed intelligence of Siemens Corporate Technology. Furthermore, Christoph Legat is currently working towards his doctoral thesis focusing on fault-tolerant field level automation software by dynamic reconfiguration in a close cooperation with the Institute of Automation and Information Systems of the Technical University of Munich, Germany. He is involved in various public funded research projects addressing monitoring and operational control aspects of production lines, product-driven automation and energy-efficiency in manufacturing automation. During the last three years, he has authored more than fifteen international conference and journal publications as well as several national and international patents. His research focuses especially on the application of formal methods and knowledge-based techniques to improve the flexibility and changeability of manufacturing control systems.
Abstract: Global and lean supply chains subject manufacturers to sudden disruptions of different severity that affect shops floors and performance. Due to a variety of factors, disruptions do not only occur internally but also externally. Hence, if manufacturers want to ensure competitive performance in a highly dynamic environment, they have to be capable of quickly detecting disruptions and adapting their production adequately. In order to detect external disruptions before its effect will manifest on-site, a novel standardized architecture for coupling manufacturing operations with an EPCIS-compliant real-time tracking & tracing system is presented. The system leverages logic-based complex event processing for detecting critical disruptions in the supply chain and logic-based reasoning for diagnostics of the on-site production system. When detecting a critical situation, adequate compensation mechanisms for robust operation will be initiated. To provide required reactivity, the production system has to be flexible enough to mitigate the effects of unanticipated disruptions. The frequent appearance of supply and production glitches, however, highlights the inflexibility of modern supply and production systems. For this reason, novel approaches to increase the adaptability and reactivity of manufacturing control systems are investigated at Siemens. Recent results of this research will be presented. Furthermore, the impact of the flexibility of manufacturing control systems on the compensability of disturbances within different control levels from production order scheduling to field-level automation software will be discussed. Despite these advanced operation techniques, a great amount of knowledge to detect disturbances and reason about capabilities of the control system for compensation handling is necessary. To bridge the gap between engineering and operation, an integrated, knowledge-based approach to develop flexible field-level automation software, gather additional information from Plant Lifecycle Management Systems and transfer this engineering knowledge into operation will be presented.